Durch die Workshops dürfen wir immer wieder mal an wunderbaren Geschichten von Teilnehmern teilhaben, das macht das Ganze so besonders und ist auch ein Grund, weshalb uns die Kurse soviel Spaß bereiten: Neue Orte und vorallem viele interessante Menschen kennenzulernen und manchmal auch die Gelegenheit zu haben, Teil ihrer zauberhaften Geschichte zu werden!
André aus der Antwerpener Gegend in Belgien hat im Mai 2020 im Workshop 23 in Hamm teilgenommen und sich seine große CNC14 gebaut. Hier erzählt er in einem Gastbeitrag seine wunderbare Geschichte, wie er zu seiner CNC14 Fräse kam und über seine Fortschritte und Ergebnisse:

Eine Modelleisenbahn, das Projekt, das vor 40 Jahren begann
Wie es 1982 begann
Vor 40 Jahren gab es noch Hobbymagazine, wie "Selber Machen", die es in Deutschland immer noch gibt. 1982 sah ich einen Artikel über den Bau einer Modelleisenbahn für den Garten; tatsächlich waren es 2 Züge, ein Personenzug und ein Güterzug. Ich bestellte dann die Konstruktionszeichnungen für 2 Gulden, sagen wir 2 D-Mark. Eine Beschreibung und zwei Zeichnungen – doppelt A0 – von 1 mal 1,5 Metern.
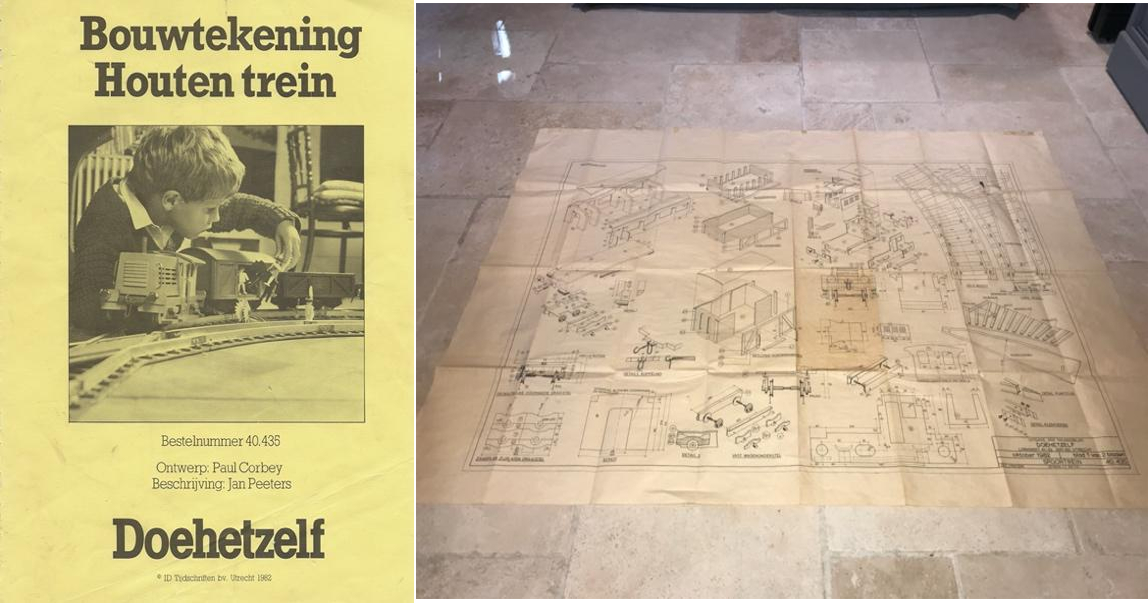
Ich dachte, das würde den Kindern Spaß machen. Ich hatte damals ein Haus, aber mit einem Mini-Garten war ich noch nicht verheiratet und Kinder waren nicht mehr als eine vage Idee. Die Konstruktionszeichnungen waren daher eine wirklich zukunftsorientierte Vision.
15 Jahre später, ca. 1997
Das nächste Haus mit wesentlich größerem Garten, verheiratet und damals 3 Kinder. Zwischen einem alten und einem neuen Job hatte ich eine 3-monatige Pause eingelegt und bin mit der Güterzug losgefahren. In der Garage, mit einer Figurensäge, einer Feile, einem Kreissägeaufsatz an meinem Bohrer und einem Black &Decker Workmate.
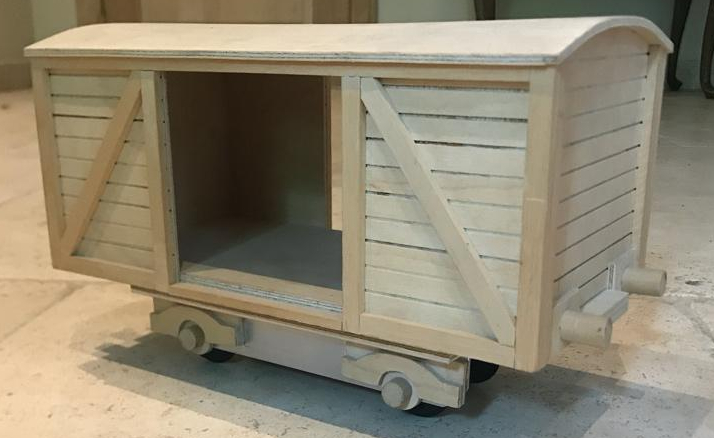
So habe ich die Rümpfe der Güterwagen gebaut. Dann begann die Arbeit und die Erziehung von Kindern die ganze Zeit zu essen und der Zug verschwand in einem tiefen Schrank.

20 Jahre später, 2020
Ich bin offiziell seit 5 Jahren im Ruhestand, habe aber jetzt auch aufgehört zu arbeiten. Es ist Zeit für ein Hobby. Reisen standen nach der Pensionierung immer auf der Tagesordnung, aber aufgrund von Corona ist dies vorerst nicht der Fall. Ein Hobby im eigenen Haus ist empfehlenswert. Deshalb bin ich wieder mit der Modelleisenbahn gefahren.
In 40 Jahren hat sich in Sachen Werkzeuge viel verändert. Die Idee war, mit CAD-Software und einem CNC-Fräser weiter aufzubauen. Ich habe schon immer im IT-Bereich gearbeitet und bin daher mit allen Arten von Software vertraut. Ich wusste nichts über das Fräsen. Nach viel Lesen und Suchen im Internet bin ich auf CNC14 gestoßen. Ich habe mich angemeldet und Ende Mai 2020 in der Workshop in Hamm meine Fräse gebaut. Wäre die Fräse einen Zentimeter größer gewesen, hätte er nicht ins Auto gepasst.
Zu Hause wurde die Fräse in einem Gartenhaus installiert, das nicht benutzt wurde. Fräsen macht viel Lärm und das ist jetzt kein Problem; wie es im Winter ohne Heizung weitergeht, werden wir sehen.

Als ich die Zeichnungen 1982 kaufte, weil ein Zug den Kindern Spaß zu machen schien, hatte ich noch keine Kinder. Jetzt werde ich die Züge beenden, aber die Kinder sind inzwischen erwachsen. Die Geschichte wiederholt sich jetzt; Ich hoffe, dass die Enkelkinder die Züge mögen werden, aber ich habe noch keine Enkelkinder.
Workflow, von der Idee bis zur Komponente
CNC (Computer Numerical Control) bedeutet computergesteuert. Der Rechner lädt ein Programm mit vorgeschriebenen Bewegungen in den Fräser und der Fräser führt diese Schritte aus. Man kann ein solches Programm selbst schreiben und am Anfang war das die einzige Methode. Heutzutage gibt es fantastische Programme, um die zu realisierende Idee visuell zu modellieren und dann in ein Fräsprogramm umzuwandeln.
Diese Programme sind wichtig: "gut started ist halb won" ist ein bekanntes Sprichwort, aber beim Fräsen heißt es eher "gut begonnen is drie Viertel gewonnen". Wichtig ist , im Vorfeld die größtmögliche Sicherheit zu erhalten, dass das zu fräsende Teil den Spezifikationen entspricht. Visualisierung ist unerlässlich.
Ein Workflow für ein Fräser besteht aus vier Schritten:
- Visuell entwickeln und spezifizieren von eine Idee: CAD (Computer Aided Design). Intern erstellt die Software ein Modell, das die Grundlage für die Anweisungen an den Fräser bilden wird.
- Umwandlung eines CAD-Modells in einen Schnittplan mit den für den Fräser auszuführenden Schritten: CAM (Computer Aided Manufacturing). Das Ausschneiden eines Quadrats ist eine einzelne Bewegung für einen Fräser, aber komplexere Teile erfordern eine Reihe von Fräspfaden. In der Regel werden die Fräsbahnen auch wieder grafisch dargestellt, um einfach zu überprüfen, was man definiert hat. Die CAM-Software kann die Fräswege in Code für eine CNC-Fräsmaschine umwandeln, "Nachbearbeitung". Dies ist oft "G-Code" nach dem Open-Source-GRBL-Standard.
- Software, um das Fräsprogramm an den Fräser zu senden.
- Der Fräser, der die Fräsbahnen ausführt, um schließlich die Idee in einem Material zu realisieren.
Wir sehen oben drei Softwarefunktionen und eine Hardwarefunktion, den Fräser. Man kann drei Programme verwenden, aber einige Programme kombinieren Softwarefunktionen zu einem. Ich selbst benutze Fusion 360, das CAD und CAM kombiniert, Candle, um den G-Code an den Fräser und den CNC14 Fräser zu senden.
In dieser Geschichte geht es nicht um Fusion oder Candle. Das sind meine Programmentscheidungen und ich gehe davon aus, dass die gleichen Dinge, die ich tue, auf ähnliche Weise wie andere Software getan werden.
Mein Projekt ist es, eine Modelleisenbahn für den Garten zu bauen. Das meiste, was ich mache, ist, flache Teile aus Sperrholz (2D) auszuschneiden; ein kleiner Teil der Arbeit erfordert die Umformung von Holzteilen (2.5D). Lassen Sie mich Ihnen ein Beispiel dafür geben.
Ich erstelle 3D-Modelle in CAD. Das ist eine Menge Arbeit und warum mache ich das und fräse dann in 2D- oder 2,5-Teilen? Ein 3D-Modell hat für mich zwei Funktionen, die visuelle Kontrolle und eine Grundlage für die Spezifizierung der 3D-Teile, die ich benötige.
Sichtprüfung
Man kann alle Teile in 2D zeichnen, ohne sie in einem 3D-Modell zu kombinieren; dann können Sie nicht visuell überprüfen, ob die Abmessungen jedes Teils auch korrekt sind.
Ein einfaches Beispiel. Machen Sie einen Würfel der Externalität 50x50x50 Millimeter mit 10mm Sperrholz. Dies sind sechs Teile, von denen vier eine Größe von 30x30x10 mm haben; die restlichen beiden müssen 50x50x10 mm groß sein, da sie auch die Seiten der anderen vier Seiten bedecken müssen.

Im linken Modell ist deutlich zu erkennen, dass die linke Seite zu groß ist und mit der unteren und die rechte Seite zu kurz ist. Dieses einfache Beispiel sollte ohne visuelles Modell vermieden werden. Für kompliziertere Projekte würde ich das nicht ohne visuelle Prüfungen ohne Fehler bekommen.
Ich arbeite mit Zeichnungen von 1982 und habe festgestellt, dass sie Fehler wie den oben im Quadrat enthalten. Hier und da hat der Zeichner vergessen, die Dicke eines Teils in die Größe des Teils einzubeziehen, das dagegen passen muss. Außerdem muss ich die Zeichnung an die Größe des Materials anpassen. Die Zeichnung verwendet 10 mm dickes Sperrholz für den Boden der Waggons, aber mein Laden verkauft 9 mm Dicke. Die Seitenwände passen gegen den Boden und bleiben unverändert; die Trennwände müssen 1 mm höher sein, da der Boden 1 mm dünner ist. Andernfalls passt das Dach nicht.
Rechts ist ein Teil des Modells eines Zugwaggons.
Visuelle Modellierung ist eine Menge Arbeit, aber es ist die Mühe wert. Beim Fräsen eines korrekten Modells können immer noch Dinge schief gehen; aber beim Fräsen eines fehlerhaften Modells kann es nie ein gutes Ergebnis geben.
3D-Sharing-Modellierung mit Software
Im Bild des Waggons sind viertelrunde Dachlamellen zu sehen. Unten springen sie hinein, um die Seitenwände zu stützen; dieser untere Teil hat weitere Aussparungen für die Trennwände. Ich habe es wie folgt gemacht.
- Machen Sie eine Zeichnung der Dachlatte und extrudieren Sie sie auf die gewünschte Länge. Dies ergibt das Ergebnis oben rechts.
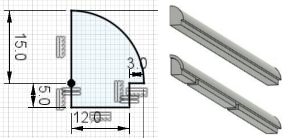
-
CAD-Software ermöglicht Operationen zwischen zwei Teilen; zusammenführen, schneiden und überschneiden. Der erste spricht für sich, der zweite schneidet einen Teil mit der Form des anderen und der dritte tut es umgekehrt und behält die Gemeinsamkeit der beiden Teile bei. Für beide Aussparungen habe ich das "Schneiden" für die Dachstange und als Werkzeug für eine Trennwand verwendet. Das Ergebnis ist absolut genau und die Teile passen perfekt zusammen. Das Ergebnis ist die Dachleiste unten rechts.
-
Es ist auch sichtbar, dass sich die Dachlamellen an den Enden einrücken, so dass sie unsichtbare Verbindungen zu den Kopfwänden bilden. Das geht auch mit dem "Schneiden". Sie sollten in der Lage sein, die Operationen selbst zu erarbeiten. Ich werde die Lösung geben. Die Kopfwand ist 9 mm dick und die Dachstange muss 4,5 mm hineinpassen. Bewegen Sie die Dachstange für die linke Seite 4,5 mm nach rechts und führen Sie das "Schneiden" mit der Kopfwand als Ziel und der Dachstange als Werkzeug durch; dies führt zur Aussparung in der Kopfwand (siehe linkes Bild unten). Bringen Sie nun die Dachstange wieder an ihren Platz – 4,5 mm nach links – und führen Sie das "Schneiden" mit der Dachstange als Ziel und der Endwand als Werkzeug durch. Dies führt zur Kreuzungskante der Dachlatte, wo sich die Seitenwand und das Dach verbinden (rechtes Bild unten).
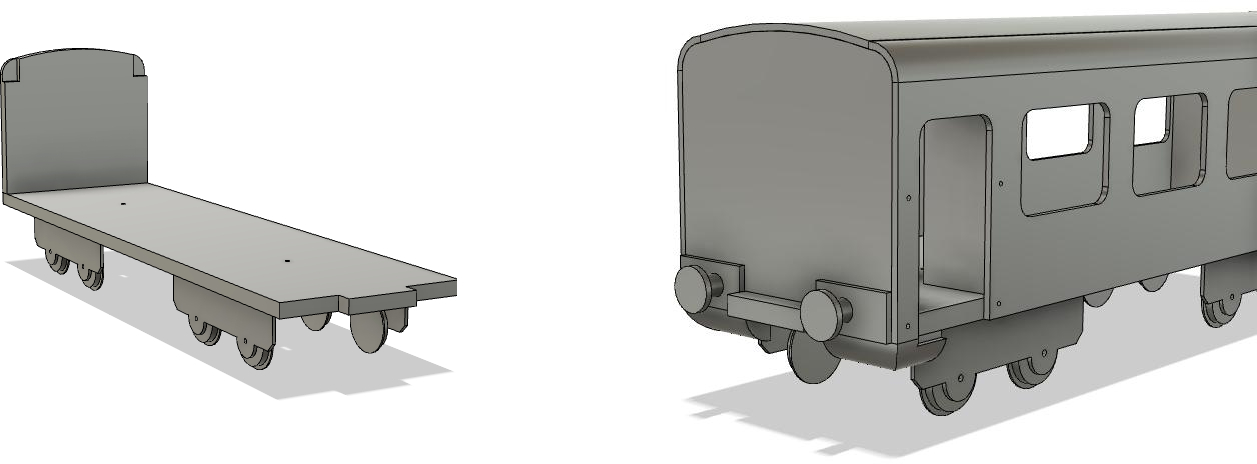
Hier ist meine Vorstellung davon, warum visuelle Modellierung das Muss wert ist:
- Um die Genauigkeit der Größen der Teile zu überprüfen.
- So bilden Sie 3D-Teile mit Bearbeitungen.
Loslegen
Fräsen der Dachlamellen
Die Dachlamellen müssen doppelt bearbeitet werden, oben und unten. Ich habe zuerst den Boden gefräst, siehe das Bild unten links. Für drei Waggons brauche ich 6 Lamellen; Ich habe 8 gemacht, für wenn etwas falsch gehen würde! Das Bild zeigt die Lamellen paarweise links und rechts zusammen.
Das untere Bild zeigt den Pfad zum Fräsen der konvexen Oberseite, eine Umrissoperation. Ich mache dies zuerst mit einem 3-mm-Fräser, der 0,5 mm weniger tief fräst als das Endergebnis, um den größten Teil des überschüssigen Materials zu entfernen. Verwenden Sie dann einen 1-mm-Fräser in die richtige Tiefe (Rest-Bearbeitung). Der 1mm Fräser würde wohl ohne die Vorbearbeitung mit dem 3mm Fräser brechen.
Zum Fräsen der Enden für die Anschlüsse an den Stirnwänden habe ich die Dachlatten hochkant bearbeitet, ähnlich wie mit der CNC14-Vise.
Rechts ist sichtbar, dass die Dachlamellen eingeklebt sind.
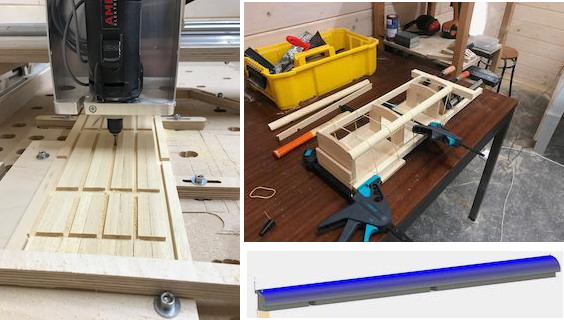
Welche Fräser
Ich verwende Birkensperrholz von 3, 6 und 9 mm und Fräsen von 3 mm und 6 mm. Ich weiß, dass ein 6mm Cutter schneller ist, aber ich habe es nicht eilig und bearbeite kleine Teile. Ein 6 mm Fräser macht viel mehr Staub als ein 3 mm und geht mir oft zu schnell. Daher in der Regel der 3 mm Fräser für die Bearbeitung von Sperrholz und der 6 mm für das Fräsen von Aluminium.
Ich benutze nur linksspiralige Fräser. Dass sie die Späne nach unten drücken, ist für mein dünnes Sperrholz kein Problem. "Normale" rechtsspiralige Fräser, schneiden unten schön und oben weniger schön; bei linksspiralen Fräsern ist es umgekehrt. Meine Erfahrung ist, dass, weil das Material an die Spannplatte geklemmt wird, die Oberseite mit einem linken Spiralfräser viel schöner und die Unterseite wenig gröber wird als bei einem rechtsspiralige Schneider. Daher meine Wahl.
2D, 2,5D und 3D
Das meiste, was ich tue, ist, Teile auszuschneiden; das ist 2D-Fräsen. In 2D legt die Z-Achse die richtige Höhe fest und dann bewegen sich nur die X- und Y-Achsen in der horizontalen Ebene. Einige dickere Teile, wie die Motorhaube der Lokomotive, haben abgerundete Seiten; Auch die viertelrunde Dachstange weiter oben in dieser Geschichte ist ein Beispiel für 2,5D-Fräsen.

Bei 2,5 Fräsen nehmen alle drei Achsen teil, aber immer nur 2 Züge gleichzeitig. Für die Motorhaube macht der Cutter einen 90-Grad-Kreisbogen mit der X- und Z-Achse. Dann verschiebt sich die Y-Achse leicht und der Viertelrundbogen wiederholt sich, bis die volle Länge zurückgelegt wird.
Beim 3D-Fräsen bewegen sich alle 3 Achsen gleichzeitig; Beispiele dafür habe ich in meiner Modelleisenbahn nicht.
Der Güterzug
Der Güterzug besteht aus einer Lokomotive und drei Waggons, einem offenen, einem geschlossenen und einem Rongenwagon. Die Lokomotive ist keine echte Lokomotive, sondern eine Rangierlokomotive, die von der Niederländischen Bahn in der Zeit von 1930 bis 1950 eingesetzt wurde. Damals wurden noch Dampflokomotiven eingesetzt. Beim Rangieren und Zusammenbauen von Zügen war es nicht praktikabel, für jede Bewegung eine Dampflokomotive aufzuheizen. Dafür waren diese kleinen Rangierlokomotiven da.
Diese Lokomotive erhielt den Spitznamen "Der Spitzbart" (einer Ziege); angeblich, weil der Klang des Signalhorns das Blöken einer Ziege ähnelte. Da der ‚Sik‘ nie auf gewöhnlicher Strecke fuhr, konnte er mit niedrigen Trittbrettern sehr niedrig gebaut werden; der Rangierer konnte also problemlos aussteigen, um Wagen zu verbinden. Er konnte der ‚Sik‘ auch von außen bedienen.
Neben einem Foto meines Modells sehen Sie auch ein Foto eines echten Sik (© Eisenbahnmuseum, Niederlande). Die großen gelben Hebel sind für den Außenbetrieb.
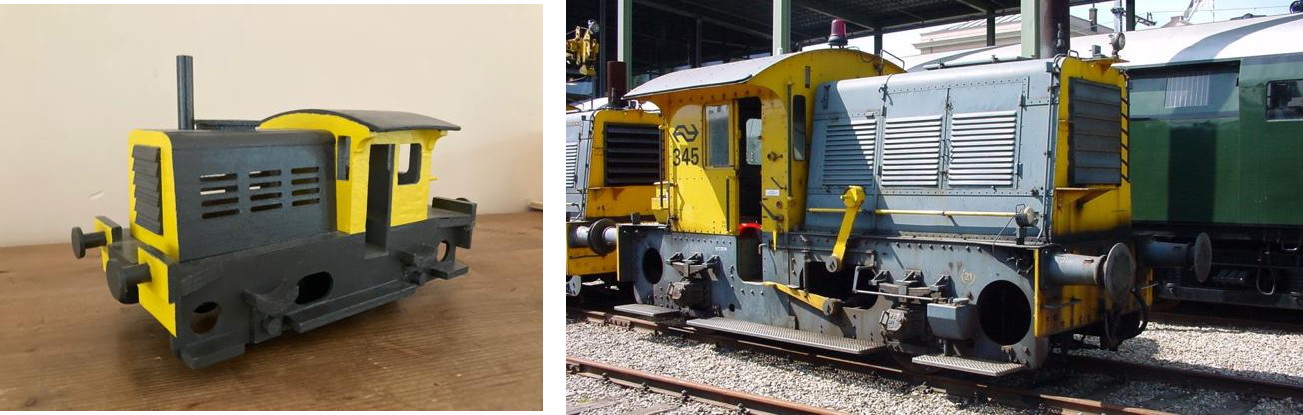
Mit dem Güterzug hatte ich bereits circa 1997 begonnen, siehe Bild am Anfang dieser Geschichte. Aufgrund der Geschäftigkeit mit Kindern und der Arbeit verschwand dieses Projekt dann im Schrank. Ich bin jetzt erstaunt, was ich damals mit Hand und begrenzten Werkzeugen erreichen konnte. Ich habe die fehlenden Teile jetzt mit der CNC14 gemacht. Unten sind einige Bilder der Konstruktion; die ersten beiden zeigen, wo ich vor 20 Jahren aufgehört habe.

Ich habe die Radsätze aus 1,5 mm Aluminium hergestellt. Mit einem 6 mm Cutter, einer niedrigen Vorschub und einer Kühlung mit Alkohol ging das sehr gut. Schutzbrillen sind notwendig, weil die Metallchips bis zu Ihren Haaren reichen!
Auf dem ersten Bild kann man sehen, wie ich 6 Radplatten gleichzeitig fräse; die daneben zeigt das Ergebnis an. Ein Laufradsatz besteht aus zwei Seiten und einer Platte. Ich hatte eine Form gemacht, um die Löcher um die Oberseite und die Seiten mit M3-Schrauben zu verbinden und für die Wellen genau mit einem 3mm Bohrer zu machen; die unteren beiden Bilder zeigen das.
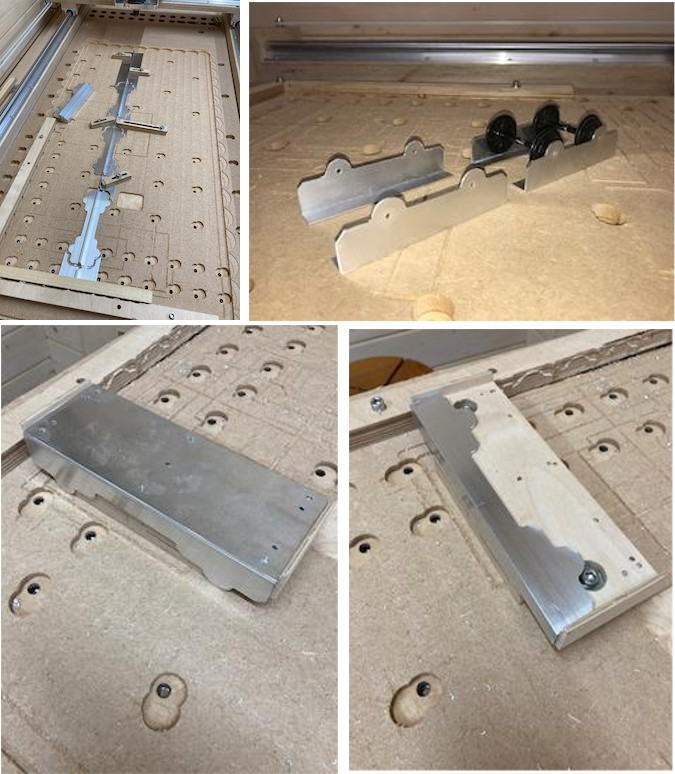
Aluminium schön von Hand zu lackieren ist praktisch unmöglich. Die Oberfläche muss geätzt werden, damit die Farbe gut haften kann. Ich ließ die losen Teile auf eine Autolackierer sprühen; er hatte wegen Corona nichts zu tun!
Bei den Waggons werden die Radsatzlager und die Aufhängung an der Außenseite der Radsätze mit Holzteilen simuliert.
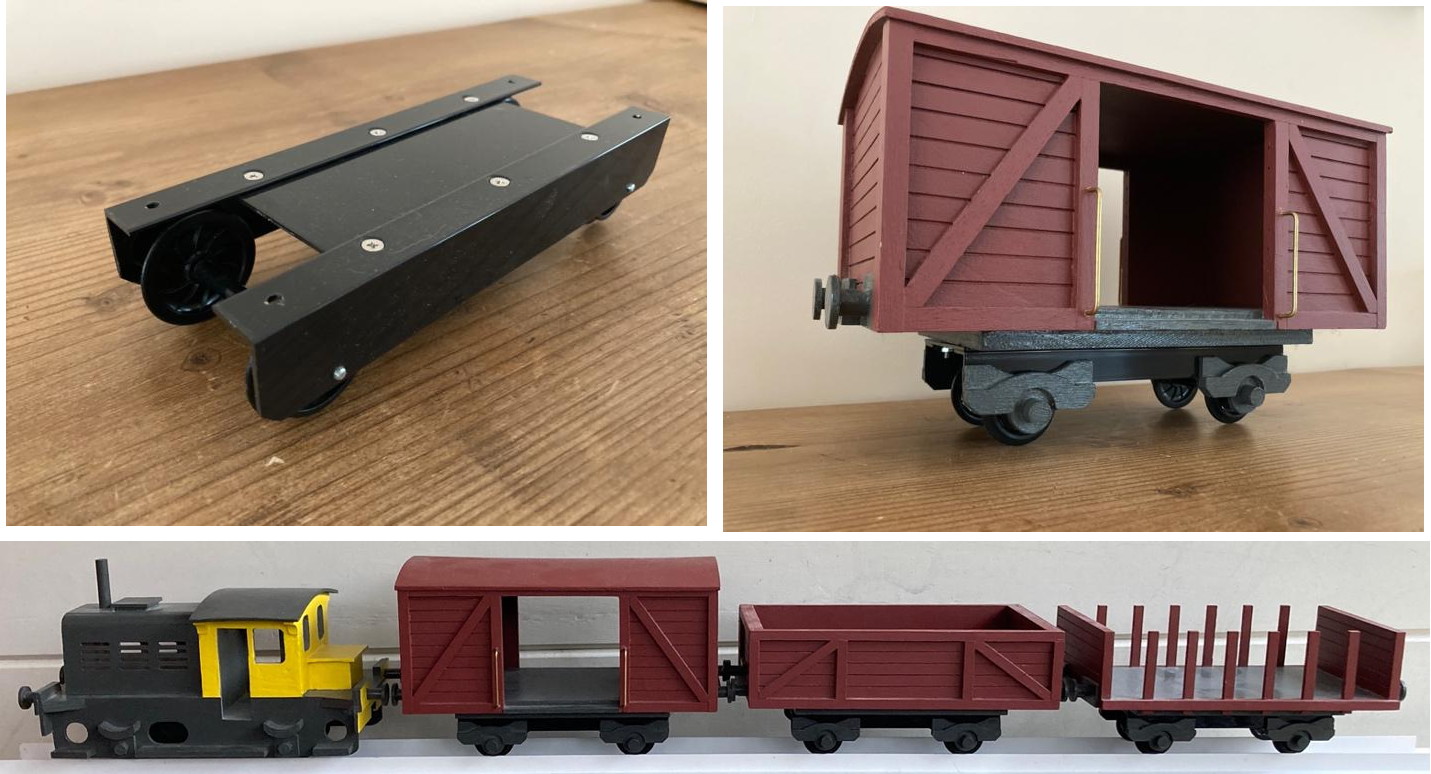
Der Personenzug
Der Personenzug besteht aus einer Lokomotive und drei Waggons für Fahrgäste. Ich entwarf einen Wagen als Wagen mit einem halben Fahrgastraum und einem halben Laderaum. Ich erinnere mich an solche Waggons aus meiner Kindheit. Der Laderaum könnte für Postsäcke und dringende Lieferungen genutzt werden; Sie könnten da auch Ihr Fahrrad mitnehmen.
Der Personenzug ist komplett mit CAD / CAM und der Fräser gefertigt. Ein großer Teil war das Ausschneiden von Teilen aus 9 und 3 mm Sperrholz. Einige Teile waren komplexer, wie die zuvor besprochenen viertelrunden Dachlamellen der Waggons und die gekrümmte Front in drei Teilen der Lokomotive.
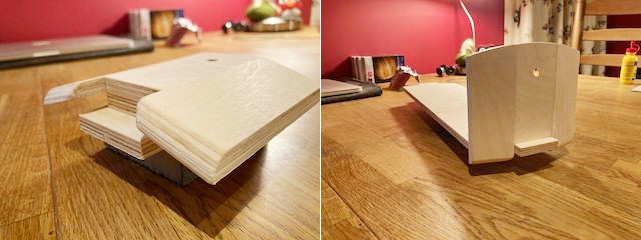
Die Teile selbst sind leicht zu zeichnen; danach brauche ich immer ein paar Tage, um eine Reihenfolge von Fräsvorgängen zu erarbeiten, die das beabsichtigte Ergebnis liefern.
Manchmal, wie bei den Teilen für die Vorderseite der Lokomotive, ist es notwendig, die Ober- und Unterseite des Teils zu bearbeiten. Dann muss man das Fräsmaterial in genau der gleichen Position umkehren können. Andernfalls passen oben und unten nicht zusammen! Ich habe dafür folgendes ausgedacht. Ich zeichne ein zusätzliches Teil, das oben und unten größer ist als das zu fräsende Teil. In diesem zusätzlichen Teil zeichne ich zwei Löcher von 8mm Durchmesser und in der Mitte der Breite. Die Mitte eines der Löcher ist der Ursprung für die Fräsbahnen.
Das folgende Beispiel zeigt nicht den Zug, sondern ein Beispiel für den Bauernhof, die ich als nächstes bauen werde. Ich hatte dieses Beispiel zur Verfügung.
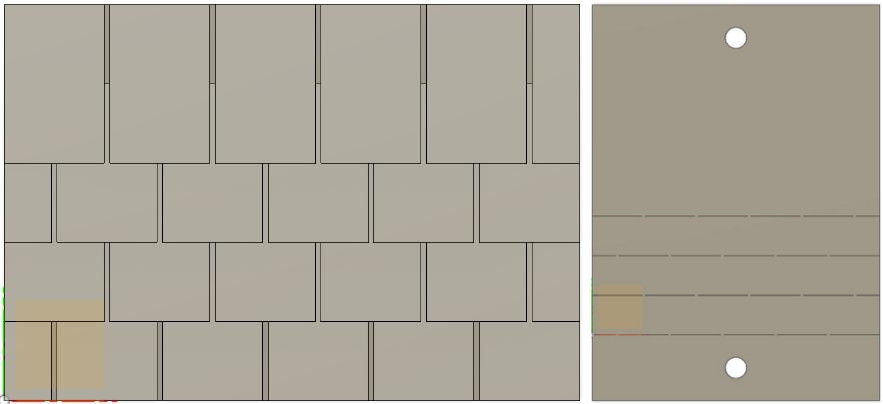
Der zusätzliche Teil dient nur zum Bohren der Löcher. Ich bohre es tiefer bis in die Opferplatte und zerschlage zwei Dübel darin. Man kann nun das Material lösen, umkehren und wieder auf die Dübel legen; durch die Dübel entspricht die Verarbeitung auf beiden Seiten exakt.
Die Waggons sind in den Farben der Belgischen Bahn bemalt (eigenes Foto ©).
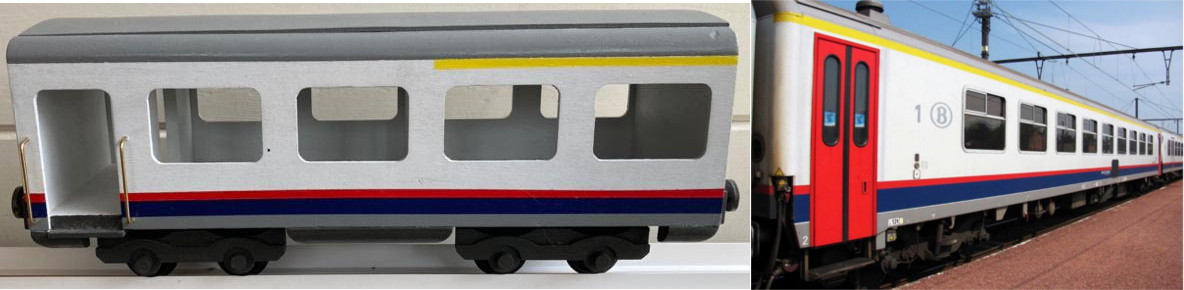
Einige Bilder der Konstruktion:
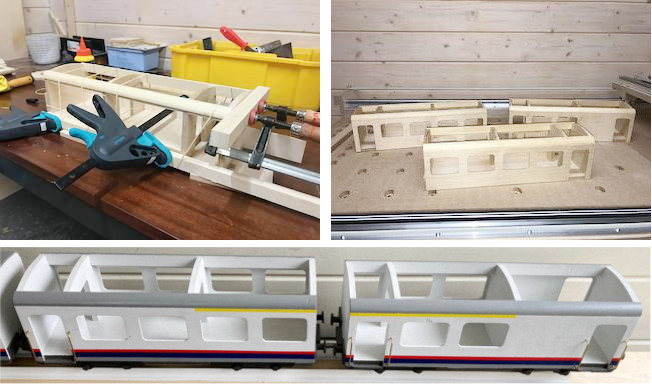
Die Wagen haben abnehmbare Dächer; dann kann ich eventuell später Sitze einbauen und Playmobil-Figuren als Passagiere verwenden.
Die Lokomotive des Personenzuges
Die Lokomotive ist noch nicht fertig. Ich werde sie später zur Geschichte hinzufügen. Das Skelett und die Querwände sind auf dem Foto zu sehen. Durch das Loch in der Vorderwand ist eine Kamera zu sehen. Ich denke, das würde den Kindern/Maschinisten Spaß machen. Die Kamera wird wahrscheinlich keine Hasen oder Eichhörnchen auf dem Bild haben, aber unsere beiden neugierigen Katzen werden auf jeden Fall ausgestellt!

Die Kamera ist mit einem Raspberry Pi verbunden, dem wohl kleinsten Linux-Computer, den es gibt (12,50 €). Die Pi kümmert sich auch um die Motorsteuerung. Die Open-Source-Software 'Homebridge' definiert den Videostream und zwei virtuelle Switches 'Forward/Backward' und 'Fast/Slow' als Apple Homekit kompatible Komponenten. Der Zug ist dann über WLAN mit einem iPhone oder iPad steuerbar. Das rechte Bild oben zeigt den Bildschirm meines iPhones mit dem Bild der Kamera.
Ende
Das Ergebnis ist unten sichtbar und ich bin stolz darauf.
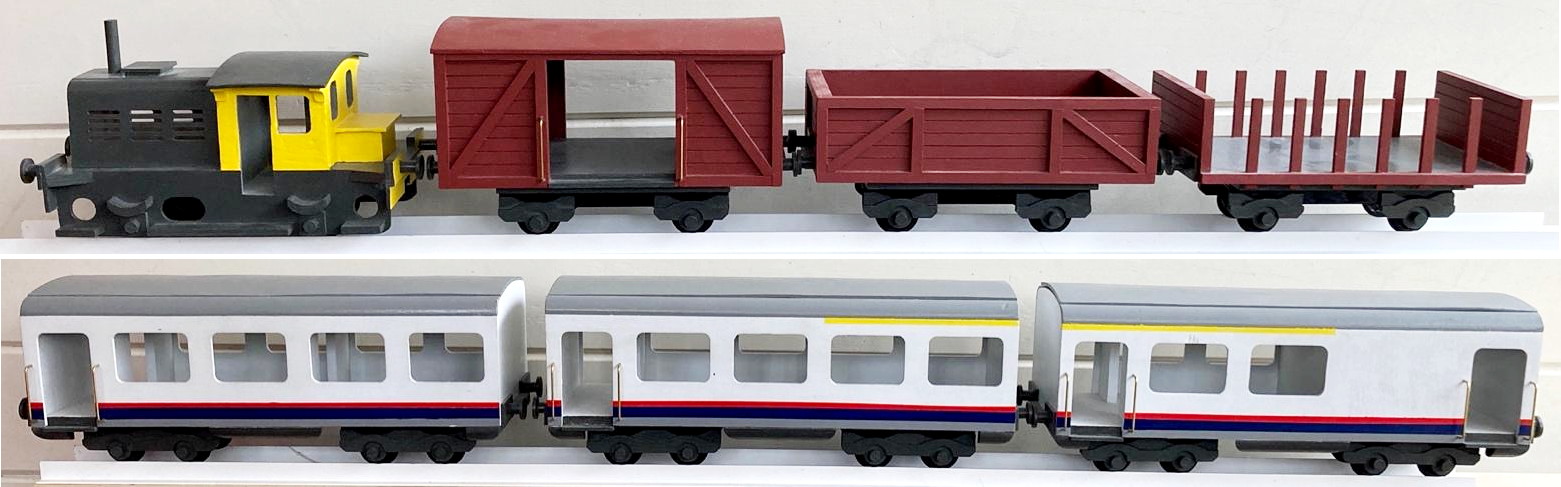
Es war eine Menge Arbeit. Der Fräser im CNC14-Werkstattgebäude erwies sich als nur der erste Schritt. Wenn Sie keinen technischen oder maschinenbaulichen Hintergrund haben, folgt nach der Konstruktion eine steile Lernkurve, um den Umgang mit CAD/CAM zu erlernen und dann Ihre Konstruktion mit dem Cutter genau zu realisieren. Wenn Sie auf der Suche nach einem Hobby sind und viel Zeit haben, kann ich nichts Besseres empfehlen, als einen Cutter zu bauen; dann ist das Zeitproblem für immer gelöst. Ich denke auch, dass man, bevor man mit dem Bau beginnt, keine Ahnung haben sollte, was man damit machen will. Ansonsten besteht die Gefahr, dass ein schöner Cutter zu wenig oder gar nicht genutzt wird. Ich hatte vor, meine Züge fertigzustellen. Jetzt, da das erledigt ist, gibt es eine Fortsetzung, weil ich auch eine Zeichnung aus dem Jahr 1975 von einer Modellfarm habe. Wie die Züge ist auch die Farm auf einer Skala von Playmobil-Figuren, so dass ich sie zusammen aufstellen kann.
Wer Fragen oder Anmerkungen hat, kann mich auf Mail an André oder über das Forum www.cnc-aus-holz.at erreichen. Letzteres ist so ziemlich eine Notwendigkeit für Anfänger; Fragen werden immer schnell und freundlich von Leuten beantwortet, die einst Anfänger waren.
Die Züge sind jetzt fast fertig. Motorisierung ist immer noch ein Wunschtraum. Die Züge sind für die Enkelkinder bestimmt; sie sind ebenso noch ein Wunschtraum, also gibt es noch Zeit, Ideen dafür zu bekommen.
-Für Inhalt, Text und Bilder verantwortlich ist André Hartman-
Vielen Dank André für diese tolle Geschichte! André kam uns auch, zwei Jahre nach seiner Workshop-Teilnahme, im Workshop 32 in Hennef besuchen und brachte seine Ergebnisse mit, sensationell! Auch wir sind stolz auf Dich André!